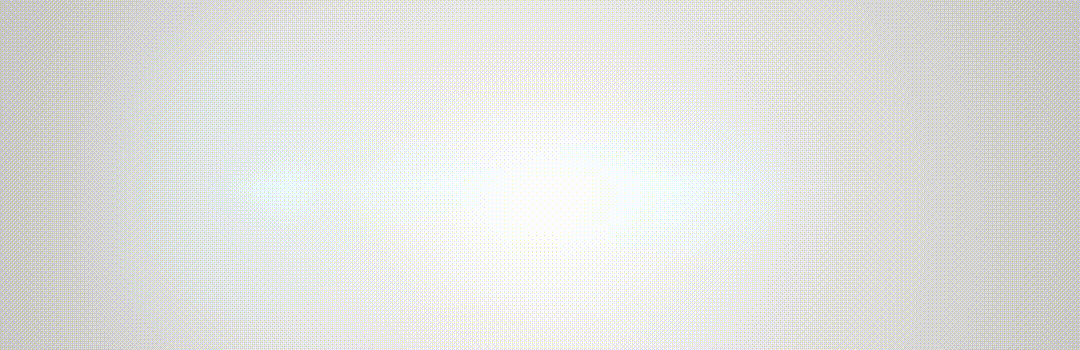

The welding robot has been calibrated for its origin position before leaving the factory, but even so, it is necessary to measure the position of the center of gravity and check the position of the tool when installing the robot. This step is relatively simple, you only need to find the menu in the settings of the welding robot, and follow the prompts step by step.
Before operating the welding robot, pay attention to check whether there is water or oil in the electrical control box. If the electrical appliance is damp, do not turn it on, and check whether the power supply voltage is in line with whether the front and rear safety door switches are normal. Verify that the direction of rotation of the motor is consistent. Then turn on the power.
Precautions for application and maintenance of welding robots
1) The use of welding robots can reduce the scrap rate and product cost, improve the utilization rate of machine tools, and reduce the risk of defective parts caused by workers' misoperation. A series of benefits are also very obvious, such as reducing labor consumption, Reduce machine tool loss, speed up technological innovation, and improve enterprise competitiveness. Robots have the ability to perform various tasks, especially high-risk tasks, with a mean time between failures of more than 60,000 hours, which is better than traditional automation processes.
2) Welding robots can replace increasingly expensive labor, while improving work efficiency and product quality. Foxconn robots can undertake the assembly tasks of precision parts of the production line, and can also replace manual work in poor working environments such as spraying, welding, and assembly, and can be combined with CNC ultra-precision iron beds and other working machines to process and produce molds to improve production efficiency and replace parts. unskilled workers.
3) The performance of welding robots has been continuously improved (high speed, high precision, high reliability, easy operation and maintenance), and the robot controller system has also developed in the direction of PC-based open controllers, which is convenient for standardization, networking, and device integration. The degree of improvement, the control cabinet is becoming smaller and smaller, and the modular structure is adopted: the reliability, operability and maintainability of the system are greatly improved, and the role of virtual reality technology in robots has been developed from simulation and rehearsal to process control. For example, the operator of the remote control robot can operate the robot with the feeling of being in the remote working environment.
When the welding robot needs to be dismantled, turn off the power supply of the manipulator; turn off the air pressure source of the manipulator. Remove air pressure. Loosen the fixing screws of the cylinder fixing plate and move the arm so that it is close to the arch. Move the bumper mount closer to the arm. Tighten the pull-out cylinder fixing plate so that the arm cannot move. Lock the rotation safety screw so that the manipulator cannot rotate, etc. These details should be paid attention to.
Yooheart welding robot application
Post time: Jun-15-2022