Is the welding positioner useful for welding robots?
Welding positioners are generally used in the industrial field and are used in conjunction with welding robots. Welding positioners are often paired with manual welding, semi-automatic welding machines, automatic welding machines, etc. to help improve welding efficiency and stabilize quality. Many users are worried about welding The role of the positioner
The positioner, also known as the flip table and the positioner, plays the role of changing the position of the workpiece in the welding work. Welding positioner is divided into seat type welding positioner, L-shaped welding positioner, double-axis welding positioner, three-axis welding positioner, etc. Users choose welding positioner to confirm the size and weight of their welding parts And what brand of robot to use.

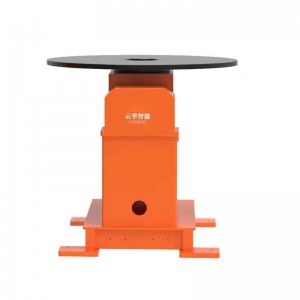
The role of the welding positioner on the welding robot:
High precision: The welding positioner can turn the workpiece to the ideal welding position, improve the distance compensation between the welding torch and the welding seam, realize precise welding, and stabilize the welding quality. The welding positioner adopts RV reducer, and the repeatability of the positioner can reach 0.1 mm.
Long service life: The simple drive system can reduce the risk of failure, and the welding robot can improve the production efficiency.
The welding positioner and the welding robot realize coordinated motion, and a control system with coordinated control function is used to control them uniformly. The welding positioner and the welding robot have asynchronous coordinated motion and synchronous coordinated motion. The synchronous coordinated motion makes the welding robot and the welding variable. The position machine runs at the same time, which can weld more complex workpieces.
The main function of the welding positioner is to turn the workpiece during the welding process, so as to obtain a good welding position, which can meet various welding quality and appearance requirements.
The base of the positioner is welded by thickened profiles and steel plates, and after annealing treatment, the quality and accuracy are reliable.
The turning is driven by a servo motor, and the reducer adopts a high-precision reducer, which has reliable precision and adjustable speed.
Liberate labor. The welding positioner is controlled by the welding robot, and the control system realizes unified control. The operator only needs to stand on the assembly station and hold the teach pendant away from the welding range. The welding positioner can automatically drag the weldment. , showing the welding seam, and the welding robot can realize automatic welding.
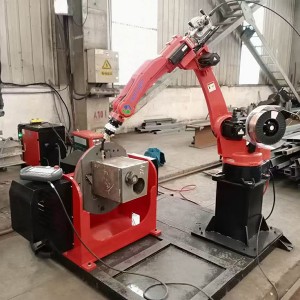
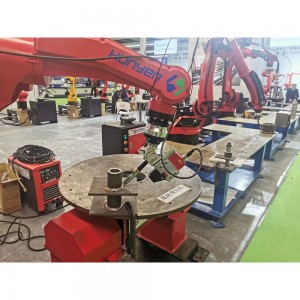
As a kind of mechanical equipment, the positioner is often seen on large construction sites. How to choose the positioner?
1. Functional requirements for displacement machinery
Refers to what action the displacement machine should be able to achieve, such as translation, lift or rotation. If it is translation, is it linear translation or curve translation; if it is rotary motion, is it continuous rotation or intermittent flipping, etc.;
2. Requirements for movement speed
It must be clear whether it is fast or slow, constant speed or variable speed, stepped or continuously variable;
3. Requirements for transmission stability and accuracy
The positioner used for automatic welding requires high transmission accuracy, and worm transmission and gear transmission can be selected at this time;
4. Requirements for self-locking, overload protection, vibration absorption and other capabilities
In general, for lifting or turning over, and for transmissions with danger of overturning, for safety, the transmission mechanism must have self-locking ability. There may be multiple transmission modes and their corresponding transmission mechanisms. At this time, it is necessary to comprehensively consider the transmission power, compact size, transmission efficiency and manufacturing cost between them.
Post time: Sep-01-2022