The welding effect of robot welding is affected by many aspects. Many customers will encounter some problems more or less before they are proficient in using welding robots. Basically, these problems are caused by improper operation or improper robot settings, and they can be solved with appropriate adjustments. Next, the editor will take you to take stock of some problems that often occur in the use of Yunhua welding robots and related solutions.
1. Unsuccessful arc starting during welding
1. The arc has not yet started
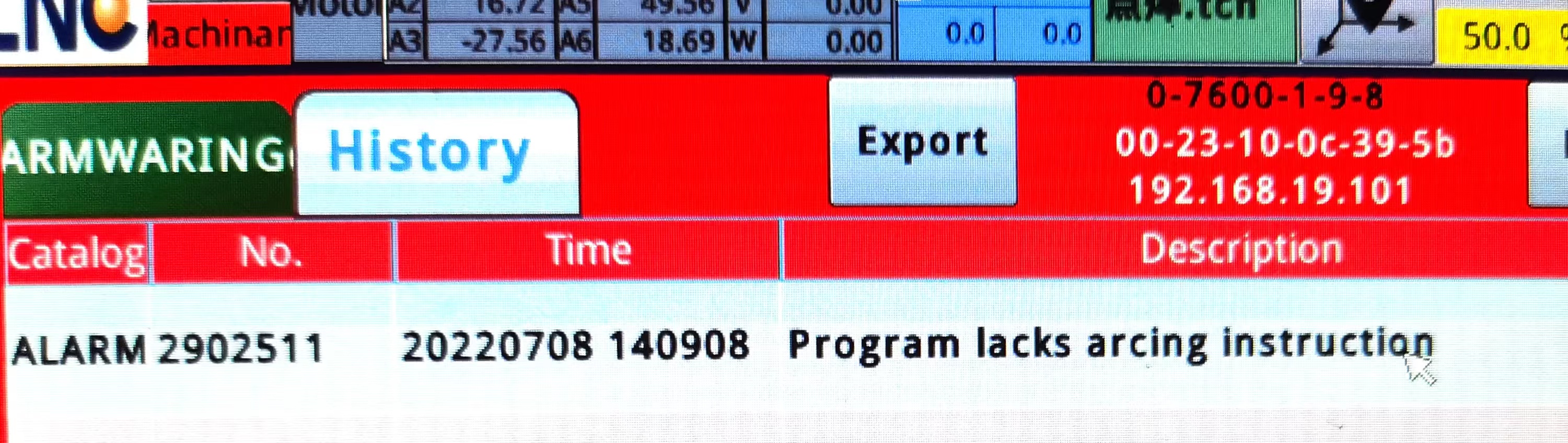
Reason: There is no corresponding arc starting command before executing the arc ending command in the edited program
Processing method: Check whether to add one more arc ending command or one less arc starting command
2. Failed to start arc, the signal detection is wrong
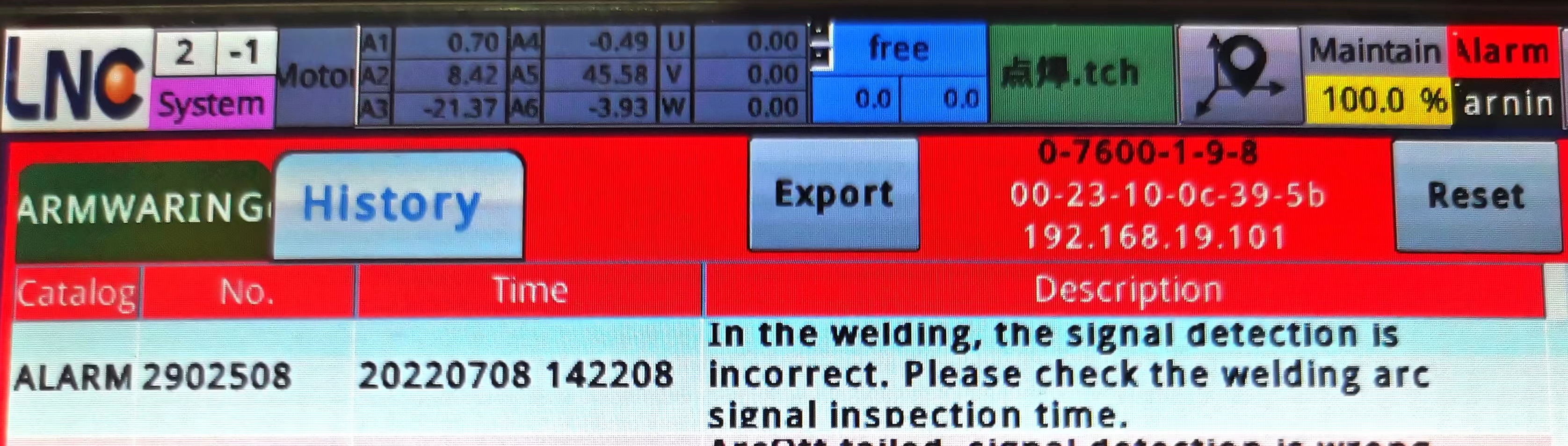
3. Arc Fried Wire
reason:
1) Current and voltage mismatch
Processing method: We need to set the appropriate current and voltage according to the actual thickness of the workpiece and the welding machine
2) The length of the welding wire is too long
Treatment method: Generally, the length of the welding wire is 10 to 15 times the diameter of the welding wire, and the appropriate length of the welding wire is selected according to the diameter of the welding wire.
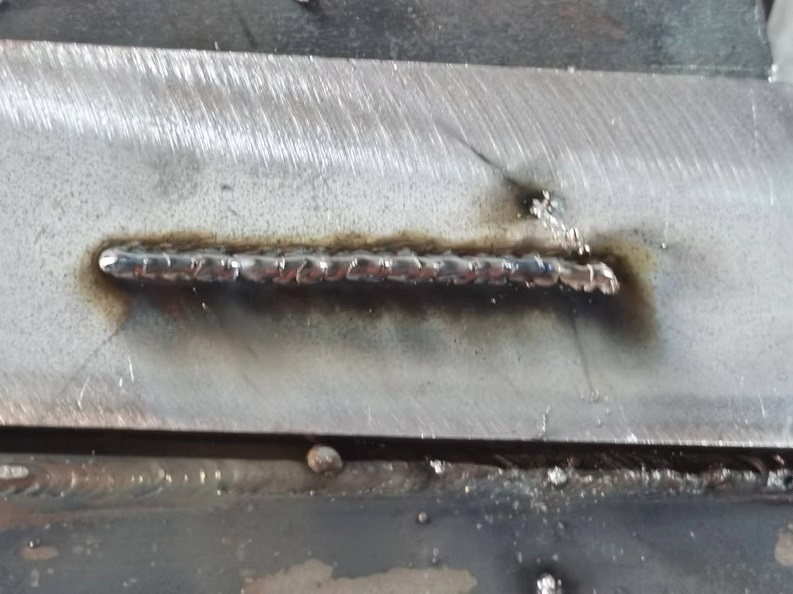
Too little current leads to uneven welds
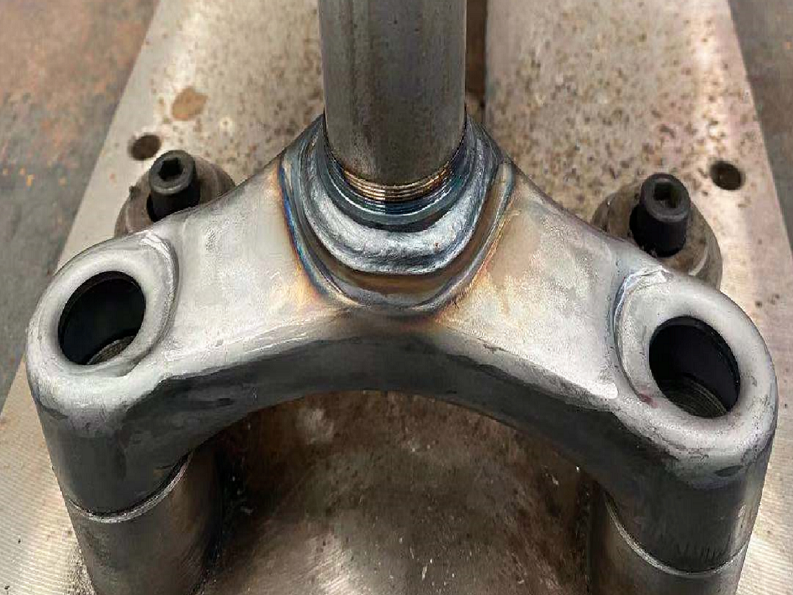
Normal current and voltage, beautiful and firm weld
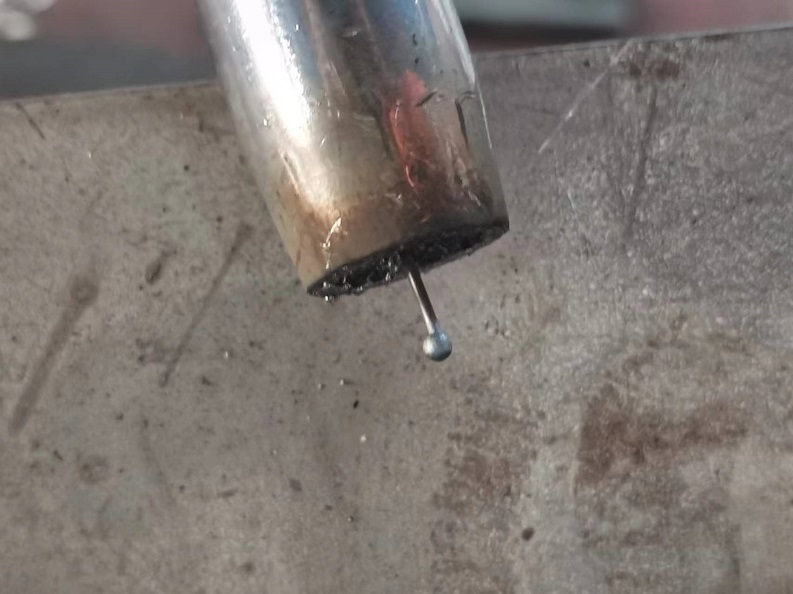
The end of the welding torch will ball the wire
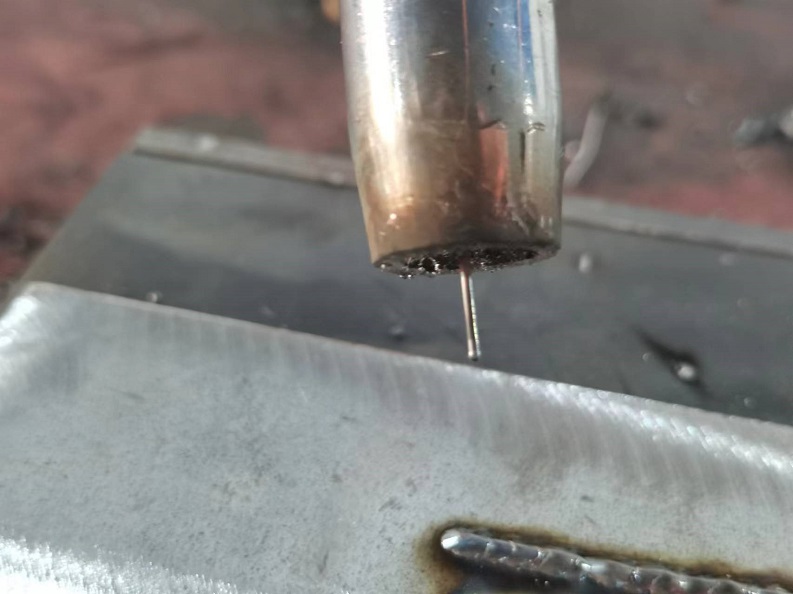
The welding torch end wire is in good condition after normal welding
4. The phenomenon of automatic arc extinguishing occurs after arcing
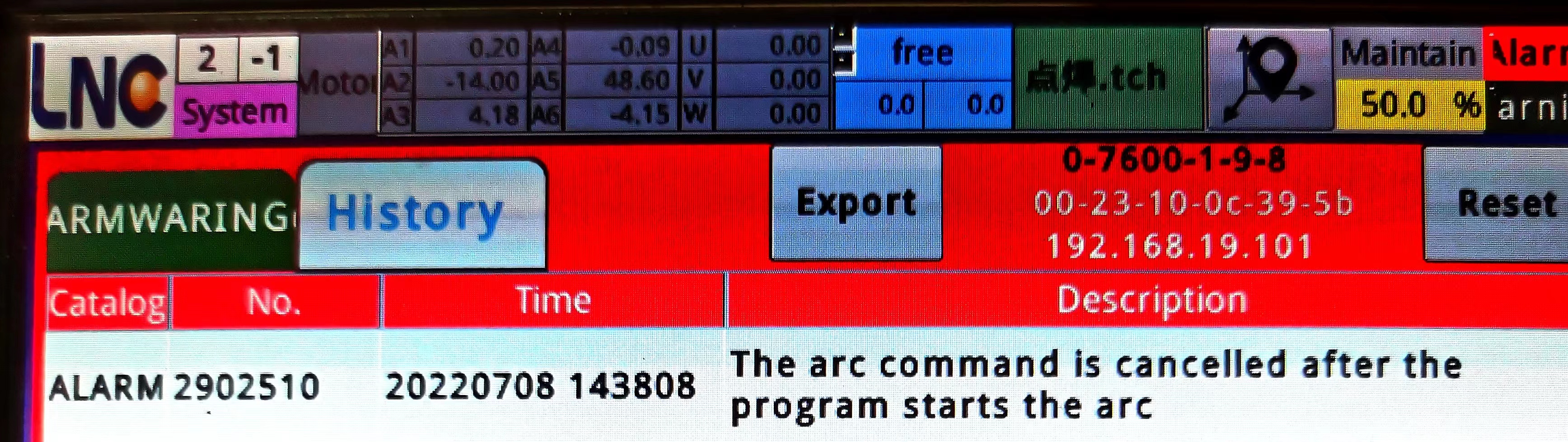
Solution: Check whether there is a problem with the parameter time not moving time setting, and check whether the welding torch has moved.
2. Arc break occurs during welding
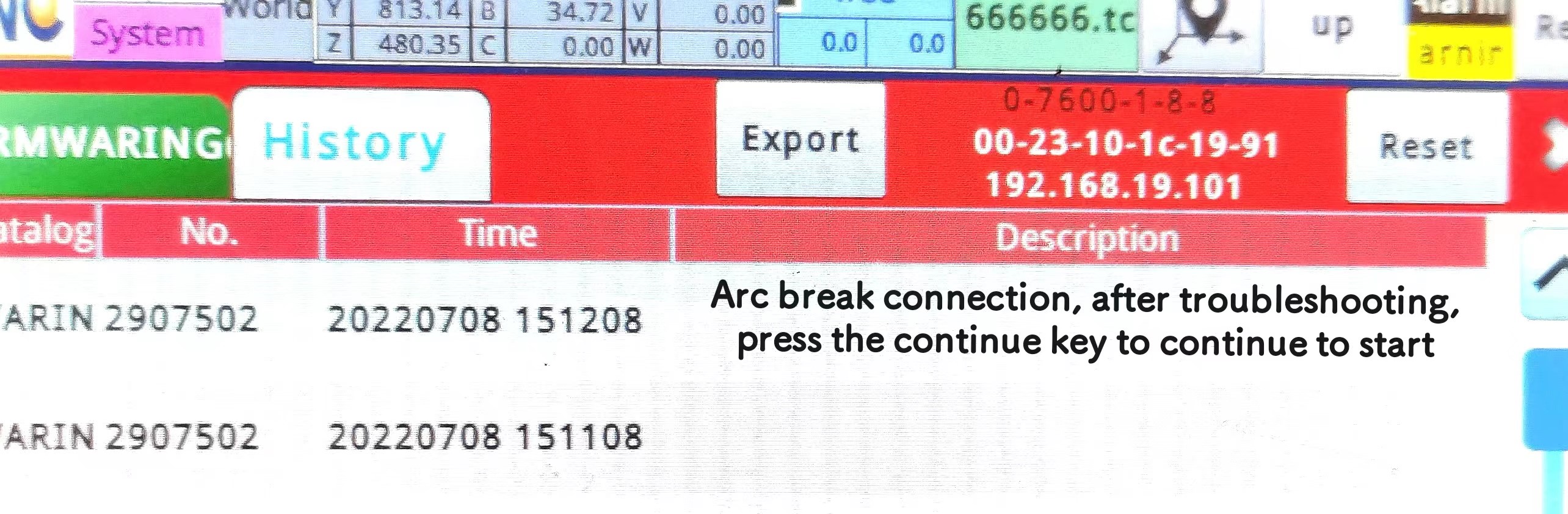
reason:
1. If the welding wire does not touch the workpiece, the arc breaking alarm will be triggered
Treatment method: Readjust the position of the welding wire and the workpiece, so that the welding wire fully contacts the workpiece during the welding process. (But it should not be too close to the workpiece, it may lead to welding through the workpiece)
2. The unreasonable welding path causes the gun head to automatically rise due to collision
Solution: reset the welding path
3. The positive and negative wires of the welding machine are in poor contact
Treatment method: Check the wiring condition of the positive and negative wires
3. Reasons for the failure of arc ending after welding
1. Arc failure, signal detection error
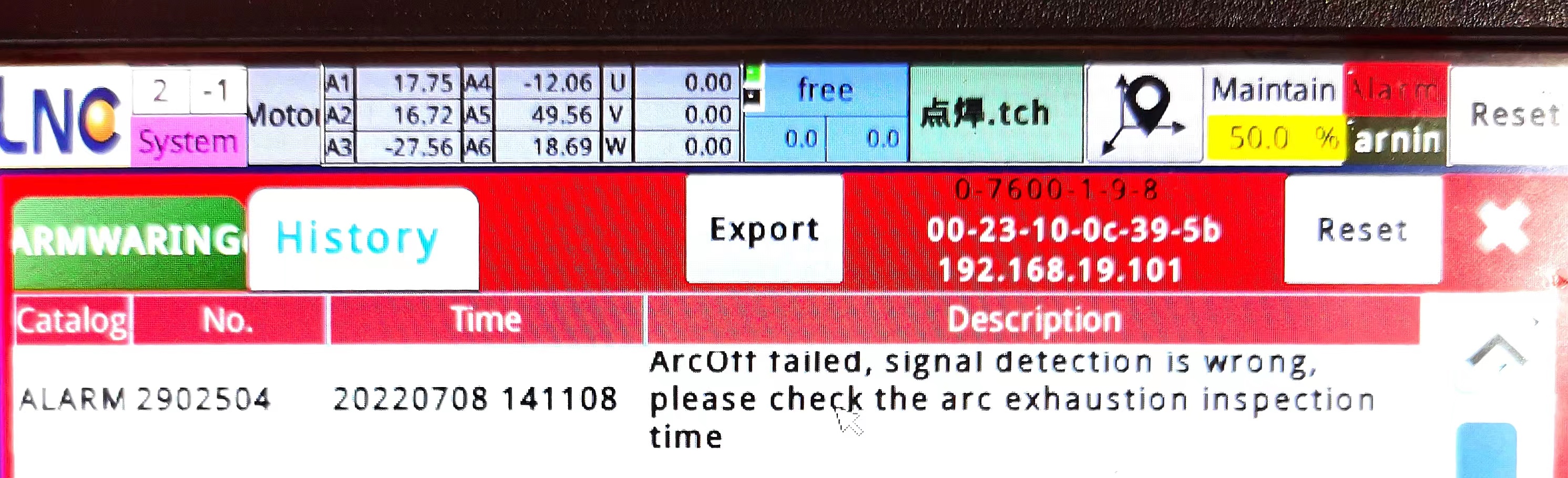
Reason: The welding machine did not receive the signal from the robot, which caused the robot to fail to close the arc.
Approach:
(1) Check whether the setting parameters are reasonable
(2) Check the IO signal, and check whether the signal of the terminating point I is abnormal. If the I point signal keeps showing ON.
(3) Check whether there is a short circuit in the line and whether the ground wire is connected abnormally
2. No arc stop command is set after arc strike
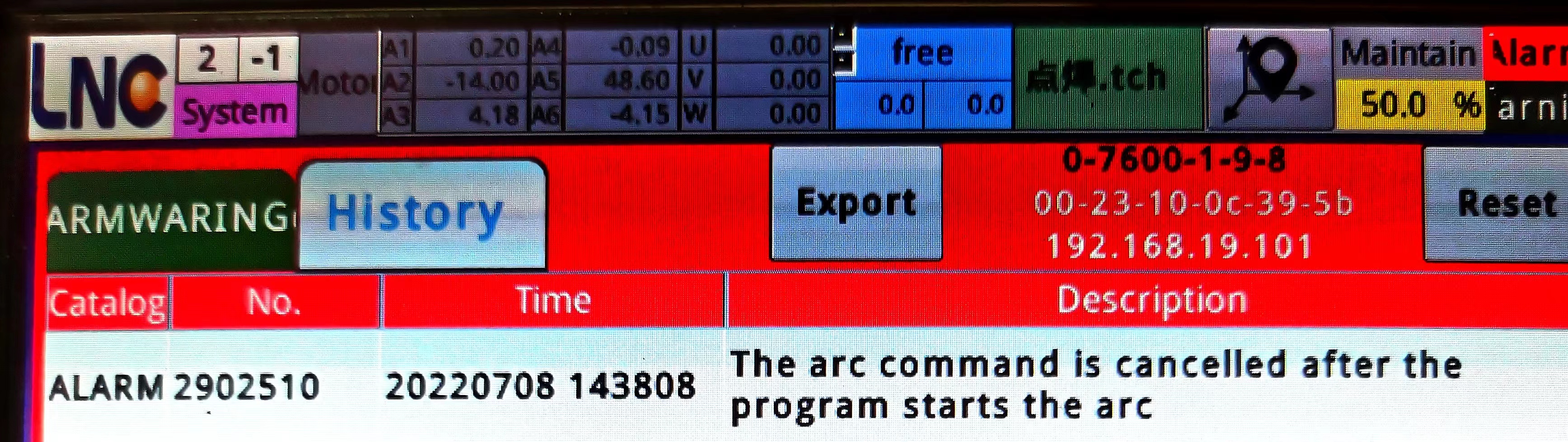
Reason: When this alarm occurs on the teach pendant, check whether you forget to add the arc ending command
Processing method: add an arc ending command after the arc starting command in the program
This issue mainly introduces the arc-starting, arc-breaking and arc-ending related problems of Yunhua welding robot during the welding process. If users encounter such problems during use, they can refer to the solutions. If they cannot be solved, please seek Yunhua technicians in time. help.
If you want to know more common problems and solutions of Yunhua Robot, please pay attention to the Yunhua Robot Official Account.
Yunhua welding robot is an automatic robot that integrates multi-functional welding such as gas shielded welding, argon arc welding, plasma cutting, and laser welding. It has high flexibility, strong adaptability, efficient welding efficiency and stable welding quality, and can be widely used in various fields. Such as machinery manufacturing, automobile manufacturing, precision electronics and coal mining and other fields.
Post time: Jul-15-2022